Transform Your Sales Team with Expert Training and Consulting.
What is Logistics?
Logistics is vital to a business as it ensures efficient operations, reduces costs, and supports timely delivery of products. It enhances customer satisfaction by meeting delivery expectations, provides a competitive advantage through better service, and optimizes supply chain management. Additionally, effective logistics aids in inventory control and enables global expansion, making it essential for business growth and success.
What is Reverse Logistics?
Reverse logistics involves moving goods from the customer back to the seller or manufacturer for returns, repairs, recycling, refurbishment, or disposal. Unlike traditional logistics, which focuses on delivering products to customers, reverse logistics manages the process after a product reaches the end of its lifecycle or requires a return.
Logistics and Reverse Logistics Management.
Below are the key procedures for reverse logistics:
Returns management.
Returns management, the most common reverse logistics process, focuses on handling customer returns efficiently. It should provide a seamless, hassle-free experience to enhance customer loyalty and strengthen brand reputation.
Return policy and procedure.
This policy serves as the standard by which all customer returns are evaluated and should be consistently followed by both customers and employees. It is best practice to keep these policies clearly visible and easily accessible to customers.
Remanufacturing or refurbishment.
Reconditioning returned products helps organizations and retailers retain profit by addressing defective items, while also reducing unnecessary waste.
Packaging management.
Organizations with effective packaging management processes can reuse packaging to reduce waste and save costs that would otherwise be spent on new packaging for returned items.
Unsold products.
Focused on returning items from end users or fulfillment centers to manufacturers, the process of returning unsold products is typically driven by factors such as delivery refusal, poor sales, or other considerations.
End of service life.
Certain products must be returned at the end of their useful life to allow manufacturers to manage proper environmental disposal.
The Logistics and Reverse Logistics process.
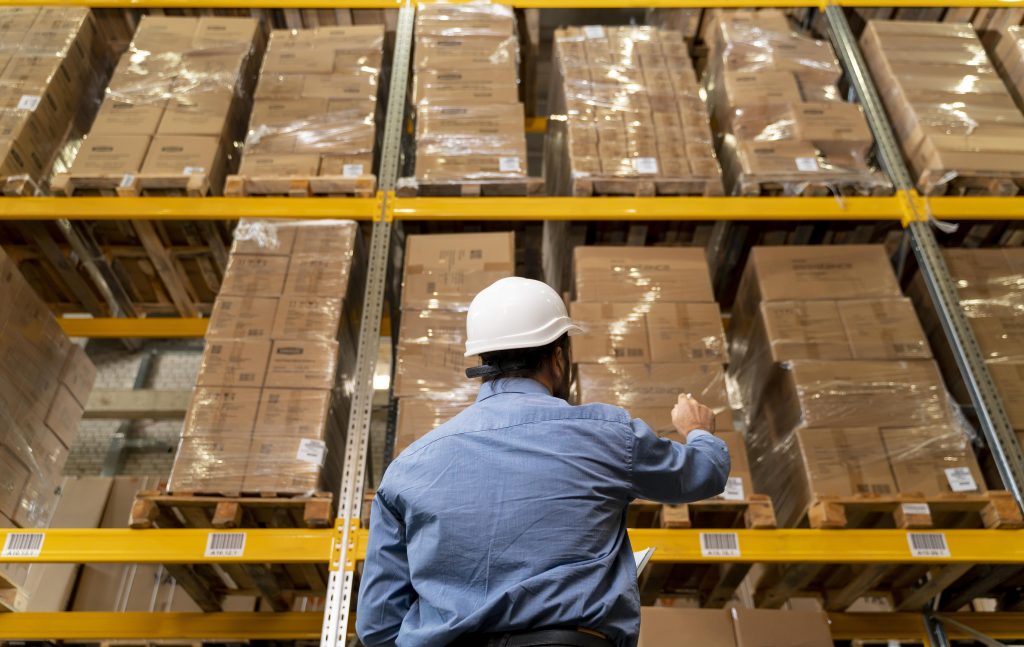
The process for managing returns varies depending on the type of reverse logistics involved, as well as the business and industry. For instance, a clothing retailer typically handles generic customer returns, while a coffee pod manufacturer might offer a mail-back recycling program for used pods. Breweries use reverse logistics to recover keg canisters for cleaning and refilling. Each business should establish a well-defined process to ensure maximum efficiency and leverage any incentives for streamlining reverse logistics, thereby enhancing environmental sustainability.
The stages of Logistics and Reverse Logistics process.
Process the returned items.
When customers initiate a return, the organization must activate its return process and follow its standard operating procedures. Every company handling returns needs a clear, organized method for managing the process. This involves outlining the step-by-step journey of returned items once they leave the customer or end user. Defining this stage helps organizations minimize unnecessary waste and pollution caused by uncoordinated logistics.
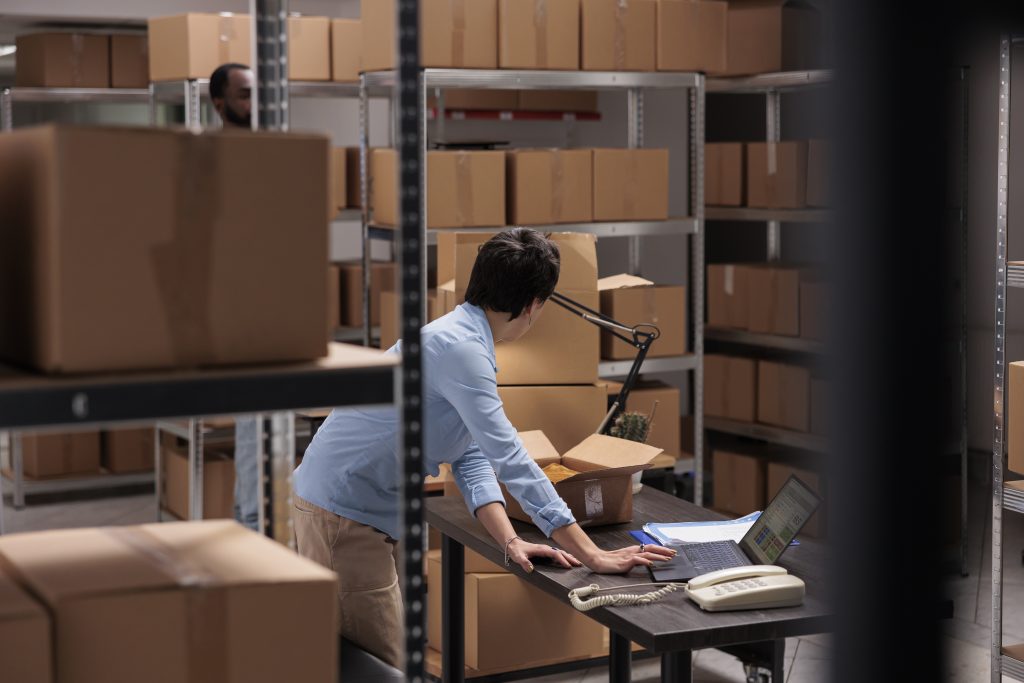
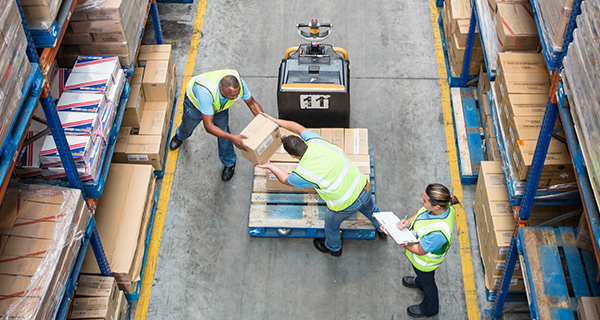
Move products to reduce waste.
Keeping returned products in motion is essential for reducing waste that results from prolonged storage. Items requiring repairs should be promptly directed to the repair department to avoid delays. Similarly, products slated for disposal or resale should be quickly moved to their designated areas, ensuring they continue through the necessary stages of the supply chain.
The goal of successful Logistics and Reverse Logistics.
Optimizing reverse logistics, regardless of your organization’s type, can yield significant benefits for both your business and the environment. The goal of effective reverse logistics is to maintain product circularity, ensuring that manufacturing, distribution, shipping, returns, repairs, and disposal operate in harmony within a continuously efficient model. This approach not only reduces costs for organizations and their customers but also minimizes the volume of products that end up in landfills. By developing and implementing a strong reverse logistics plan, your organization can create additional value for customers, demonstrating how you manage these essential processes sustainably.
Optimize your reverse-logistics strategy.
Optimize your reverse logistics strategy with the ASCM Certified in Logistics, Transportation, and Distribution (BTA) program. Professionals who earn the BTA designation are equipped with the knowledge to implement industry best practices, reducing unnecessary costs and product waste. To learn more about this certification, visit our product page.
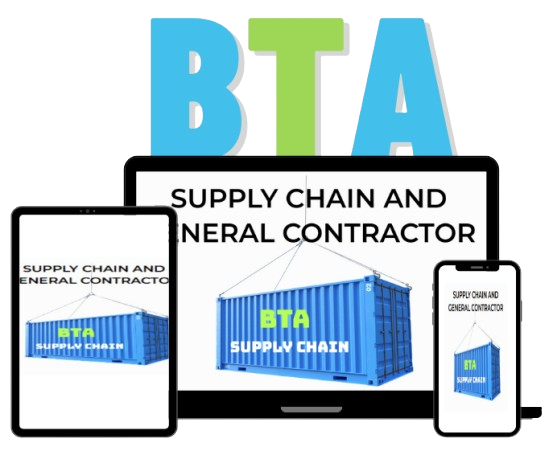
Frequently Ask any question.
When customers initiate a return, the organization must then initiate the return process and put their standard operating procedure in motion. Every company that deals with returns needs to have an organized method of initiating returns. This means outlining the step-by-step process that returned items will go through once they leave the hands of the customer or end user. Defining this stage can help organizations reduce unnecessary waste and pollution as a result of uncoordinated trucking.
When customers initiate a return, the organization must then initiate the return process and put their standard operating procedure in motion. Every company that deals with returns needs to have an organized method of initiating returns. This means outlining the step-by-step process that returned items will go through once they leave the hands of the customer or end user. Defining this stage can help organizations reduce unnecessary waste and pollution as a result of uncoordinated trucking.
Optimize your reverse-logistics strategy with the ASCM Certified in Logistics, Transportation and Distribution (BTA) program. Professionals who have earned the BTA designation are better prepared to implement industry best practices and help reduce unnecessary costs and product waste. To learn more about this certification, view our product page.
Our Expertise
Elevating Supply Chain Performance, Every Step of the Way.

Distribution & Logistics

Business Consulting & Strategy

Product Activation & Sales Expansion

Sales Training & Marketing Solutions

Merchandising & Reverse Logistics Services
Our Core Competencies.
Elevating Supply Chain Performance, Every Step of the Way.

Prev Next Supply Chain Strategy Practice

Prev Next Supply Chain Strategy Practice

Prev Next Supply Chain Strategy Practice

Prev Next Supply Chain Strategy Practice
Let’s Work Together.
We’re excited to help you succeed. Contact us today to explore partnership opportunities or schedule an appointment.
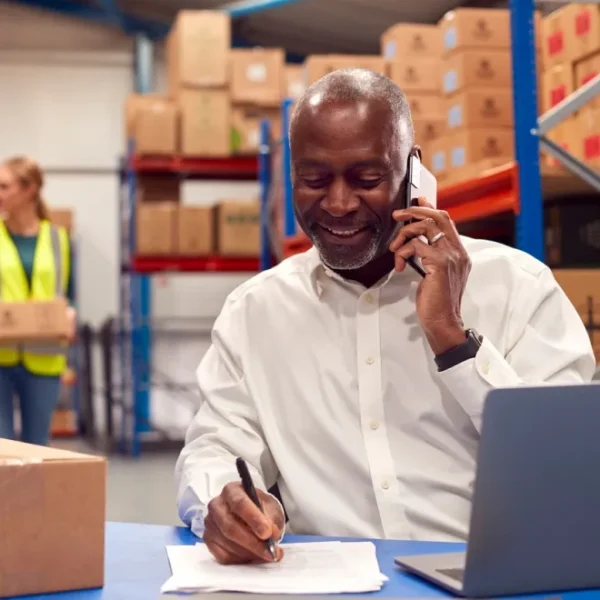